Shiloh Plastics will be closed for our Christmas Break from Monday the 23rd of December 2024 until Friday the 10th of January 2025. Last dispatch day will be Thursday the 19th of January 2024. The team at Shiloh Plastics wish you a Merry Christmas. See you again in the New Year.
Vacuum Forming Specialist
At Shiloh Plastics, our major process vacuum forming. In the early days of our business, all of our packaging was vacuum formed, and so it is an area that we have many years experience in.
Perfect for Plastic Packaging
Vacuum forming is a process that lends itself well to plastic packaging, though it has other applications as well. There are other vacuum forming businesses that specialize in making things like signs. This is a different area of expertise, and so we don’t do that kind of work. However, from time to time, people do ask us to produce something that isn’t a package, and we are able to do it.
Points to note about our process:
If you think that we may be able to make something for you, here are a few things that you need to know about our process.
- We work in light-weight material. The plastic that we usually work with is between .175mm and 1mm.
- Our machinery will allow us to vacuum form Poly Vinyl Cloride (PVC) and High Impact Poly Styrene (HIPS). The raw material that we stock is mostly either clear or white. We also have small quantities of brown and gold. Technically, any colour plastic can be folded, but you would need to be placing a very large order for us to be able to purchase a different coloured material.
- We don’t mold pre-printed plastic.
- Vacuum forming requires the use of a mold and a specially made knife to cut out the finished product. That means that when we do custom jobs, the customer will be invoiced for the cost of all tooling required.
- There are limitations in what we can vacuum form. For us to be able to cut out the formed plastic, the part that is cut needs to be flat.
- Our process involves a heated plastic sheet being sucked over a mold and then lifted off. Therefore, in order for us to remove the plastic from the mold there needs to be some taper on the sides of the mold.
- There are other limitations on what we can mold. We are happy to discuss your specific needs with you.
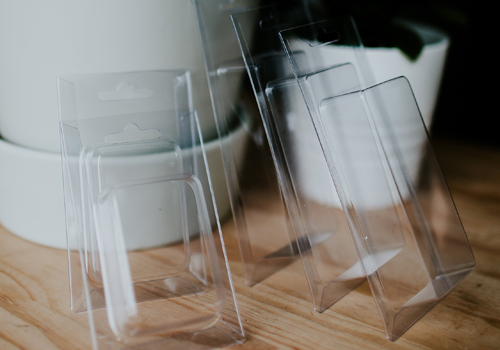